Повышение энергетической эффективности зданий промышленных предприятий в условиях Сибири
Enhancement of Energy Efficiency of Industrial Enterprises in Siberian Climate
A. S. Rubtsov, General Director LLC :Vent-Design”
Keywords: heat recuperation, waste heat, absorption chiller, energy efficiency
Enhancement of energy efficiency of an enterprise, reduction of the production cost of products and significant savings of thermal energy can be achieved through implementation of a system for recuperation of waste heat from process equipment. The article reviews a heat recuperation scheme implemented at one of Siberian enterprises and demonstrated the economic result achieved.
Повышение энергетической эффективности предприятия, снижение себестоимости выпускаемой продукции и существенная экономия тепловой энергии могут быть достигнуты в результате внедрения системыутилизации сбросной теплоты от технологического оборудования. В статье рассмотрена схема утилизации теплоты, реализованная на одном из сибирских предприятий, и продемонстрирован полученный экономический эффект.
Повышение энергетической эффективности зданий промышленных предприятий в условиях Сибири
Повышение энергетической эффективности здания, снижение себестоимости выпускаемой продукции и существенная экономия тепловой энергии могут быть достигнуты в результате внедрения системы утилизации сбросной теплоты от технологического оборудования. В статье рассмотрена схема утилизации теплоты, реализованная на одном из сибирских предприятий, и продемонстрирован полученный экономический эффект.
На территории России работает достаточно много производственных предприятий, имеющих в своем составе тепловыделяющее технологическое оборудование, использующееся для сушки и выпечки различной продукции, в том числе пищевых продуктов. Чаще всего технологический процесс может идти при достаточно высоких температурах, до +200 °C, и использует в качестве источника теплоты природный или сжиженный газ с непосредственным сгоранием внутри камер технологического оборудования. Как следствие, образуются дымовые газы с температурой выше +150 °C и, кроме того, могут присутствовать местные отсосы от прессов и сушилок с температурами вытяжного воздуха выше +100 °C.
В данной статье пойдет речь о том, как снизить себестоимость выпускаемой продукции. Уверен, что такая цель является если не приоритетной, то уж точно желаемой. В качестве примера рассмотрим одно из производственных предприятий холдинга КДВ, расположенное в Сибири. На самом деле вопрос, как хотя бы частично вернуть выбрасываемую теплоту обратно, на пользу завода, стоит на предприятии уже много лет, ведь технология потребляет значительные объемы энергоресурсов, и это сказывается на себестоимости выпускаемой продукции. Задача, которую поставил заказчик, состоит в возврате существенной части выбрасываемой теплоты для нужд отопления, теплоснабжения калориферов приточных систем, а также для ГВС.
Утилизация теплоты
Рассматриваемое предприятие площадью свыше 50 000 м? имеет в составе производственные линии, склад готовой продукции и логистический комплекс с рампой для загрузки автомашин. Рассмотрим принципиальную схему системы утилизации теплоты (рис. 1).
![]() |
Рисунок 1 (подробнее)
Принципиальная схема системы утилизации теплоты |
В сущности, система может использовать сбросную теплоту как для теплоснабжения зимой – по прямому назначению, так и для выработки холода летом. Холод в летний период может использоваться для охлаждения склада готовой продукции или приточного воздуха для выполнения технологических условий в рабочей зоне. Все температуры приведены для расчетного зимнего периода, за исключением температур на генераторе АБХМ (абсорбционная холодильная машина) [1] – здесь даны значения для летнего периода.
Начнем с зимнего режима эксплуатации. Основной потребитель теплоты зимой – приточные установки, поэтому теплоты, получаемой от т/о-утилизаторов, хватит лишь для подачи 60 000 м3/ч свежего воздуха при наружной температуре –39 °C. В менее холодный период приточные установки с управлением от частотного привода позволяют подавать 80 000 м3/ч. При температуре на улице выше –30 °C, что составляет зимой 98 % времени, в системе появляются избытки теплоты, можно их пустить на нужды ГВС или отопления. Система ГВС должна быть вспомогательной, т. е. иметь дополнительную функцию нагрева воды на предприятии. Максимальная тепловая мощность системы достигается в самые холодные дни – 1,2 МВт, минимальная – летом, порядка 600 кВт. Стоит сразу отметить, что температуры теплоносителя в водяном контуре зависят от температур антифриза в контуре калориферов приточных систем, т. е. от наружной температуры. С повышением температуры в водяном контуре снижается тепловая эффективность системы, и при максимальных температурах летом для работы АБХМ +95…+80 °C мощность снижается до 600 кВт. Если необходима максимальная производительность системы охлаждения (холод от АБХМ), мы не можем в этот период рассчитывать на получение горячей воды. В этом случае АБХМ произведет 400–420 кВт холода. Возможно, это будет происходить в пиковые жаркие дни, а в остальной период лета будет преобладать запас в виде невостребованного холода, значит, можно пользоваться ГВС от системы. Бак-аккумулятор ГВС должен проектироваться с учетом пиковых нагрузок ГВС и количества смен на предприятии или для технологических задач, и при правильном расчете можно добиться более-менее ровного потребления теплоты от системы утилизации при обеспечении покрытия пиковых нагрузок теплопотребления на бак-аккумулятор.
Стоит отметить, что, вероятно, возникнут ситуации, когда и ГВС требуется в небольших объемах, и на улице уже не холодно, а выше +10 °C, и холода на предприятии не нужно. Поэтому не обойтись без сухого охладителя К1, который включается в работу при повышении температуры в подающем водяном трубопроводе от т/о-утилизаторов выше +95 °C. Он исключает нежелательное вскипание воды и перегрев гликолевого теплоносителя. Для простоты на схеме не показаны расширительные баки, насосы подпитки, датчики системы автоматизации и прочие необходимые элементы системы.
![]() |
Рисунок 2. Часть системы дымоходов от технологического оборудования |
На рис. 2 показана часть системы дымоходов от технологического оборудования. Рис. 3 иллюстрирует вид вертикальных прямоугольных шахт, собирающих дымовые газы от нескольких производственных линий.
![]() |
Рисунок 3. Вид вертикальных прямоугольных шахт, собирающих дымовые газы от производственных линий |
Шахта № 3 отличается от первых двух, она собирает выбросы местных отсосов с содержанием паров влаги, жира и масла, поэтому здесь решено было использовать съемные очищаемые фильтры типа AirMet 610?610?50 в корпусе FCB-P 2020 GZ.
Оценка эффективности
Приведем некоторые расчеты и выводы, позволяющие оценить целесообразность таких мероприятий. Рис. 4 наглядно показывает распределение теплоты от системы утилизации по основным потребителям в зависимости от наружной температуры. Теперь, зная часы стояния наружных температур, т. е. распределение наиболее вероятного температурного графика по часам стояния, мы можем построить диаграммы, показывающие тепловую энергию в кВт•ч за год (и полезный холод) для каждого диапазона температур в году (рис. 5).
![]() |
Рисунок 4. Распределение полезной тепловой мощности по температурам |
![]() |
Рисунок 5. Распределение полезной энергии по наружным температурам, кВт·ч/год |
Остается посчитать энергию в рублях для экономических оценок. На рис. 6 приведена экономия, выраженная в рублях, для каждого потребителя тепловой энергии. Общий эффект может составить, соответственно, 4,1 млн руб. В основу расчета легли следующие тарифы на энергоносители: 1 000 м3 природного газа – 4 200 руб. с НДС, 1 кВт•ч электроэнергии – 3 руб. Таким образом, если сравнивать теплоту, получаемую от газовой котельной, то при КПД котлов 80 % и сопутствующих потерях в тепловых сетях предприятия 10 % (что далеко не самая большая величина), получаем, что 1 кВт•ч тепловой энергии стоит примерно 67 коп. Амортизацию сетей и оборудования котельной, покупку технических условий на газ учитывать не будем.
![]() |
Рисунок 6. Экономия средств за год |
Попробуем сделать некоторые выводы. На первый взгляд, наименьшую пользу приносит холод, т. к. по сравнению с классическими компрессионными холодильными машинами выгода всего 830 тыс. руб. ежегодно, а стоимость АБХМ достаточно ощутимая. Однако нужно вспомнить о технологическом присоединении к электрическим сетям. Для выработки 420 кВт холода стандартным путем необходимо примерно 140 кВт электрических мощностей. Это может обойтись по тарифу 30 000 руб. за 1 кВт мощности в 4,2 млн руб. единовременных затрат, что уже совсем не мелочь (добавим, что в подмосковных районах и Москве действуют свои тарифы). В случае модернизации производства речь идет о другой экономии: высвободившиеся электрические мощности можно использовать для развития производства, чтобы не докупать новые лимиты (или докупать в меньшем количестве). Забегая вперед, поделимся наблюдением: выгоднее проектировать систему на большую тепловую мощность; к примеру, АБХМ в 2 раза выше мощностью по холоду стоит не в 2 раза дороже, что уже намного интереснее заказчику.
Теперь предлагаем взглянуть на мощность калориферов приточных систем 1,2 МВт с точки зрения инвестиций в эту тепловую мощность при стандартном подходе – строительстве газовой котельной. Газовая котельная с тепловыми сетями до ближайших корпусов обходится инвесторам примерно в 7 млн руб. за 1 Гкал/ч тепловой мощности (что равноценно 1,2 МВт теплоты). В случае применения описываемой технологии мы вполне можем уменьшить мощность производимой теплоты традиционными способами, причем существенно.
В заключение, оценивая все показатели, можем сделать следующий вывод: данная технология окупается менее чем за 2 года. И возможно, менее чем за 1 год в случае значительных тепловых мощностей и более дорогих тарифов на присоединение к электрическим/тепловым сетям.
Литература
- Абсорбционные бромистолитиевые холодильные машины ТЕПЛОСИБМАШ (АБХМ, абсорбционные чиллеры). www.teplosibmash.ru/catalog/id/5/.
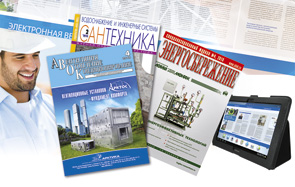
Статья опубликована в журнале “АВОК” за №8'2013
Статьи по теме
- Сравнение энергетической эффективности стальных панельных радиаторов
АВОК №3'2015 - Государственное регулирование в области повышения энергоэффективности закупок
Энергосбережение №1'2017 - Эффективный возврат теплоты на литейных заводах
АВОК №8'2014 - Повышение энергоэффективности зданий, строений и сооружений. Задачи Минстроя России
Энергосбережение №3'2015 - Зеленое строительство – комплексное решение задач энергоэффективности, экологии и экономии
Энергосбережение №3'2017 - Газоприводная мультизональная климатическая система
АВОК №3'2015 - Запуск и пусконаладка адаптивной системы вентиляции
АВОК №5'2015 - Первичная энергия как критерий энергетической эффективности
Энергосбережение №4'2011 - Оценка эффективности глубокой утилизации тепла продуктов сгорания котлов электростанций
Энергосбережение №2'2016 - Приточно-вытяжные установки для помещений жилых зданий. Европейская программа сертификации
АВОК №8'2015
Подписка на журналы
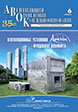
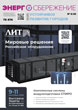
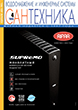